Was muss man wissen, um Maschinendatenerfassungen richtig aufzubauen?
Einer der ersten Schritte in Richtung Digitalisierung in der Industrie ist die Maschinendatenerfassung. Über vernetzte Maschinen werden Daten erfasst, gespeichert und ausgewertet. Durch die verfügbaren Daten wird eine völlig neue Transparenz geschaffen, die eine bessere Produktionssteuerung erlaubt und Potentiale in der Prozessoptimierung aufdeckt. Wir beleuchten hier die wichtigsten Grundlagen rund um die Maschinendatenerfassung in Fertigung und Produktion und zeigen in einem praktischem Beispiel die Einsatzmöglichkeiten von Maschinendatenerfassung auf.
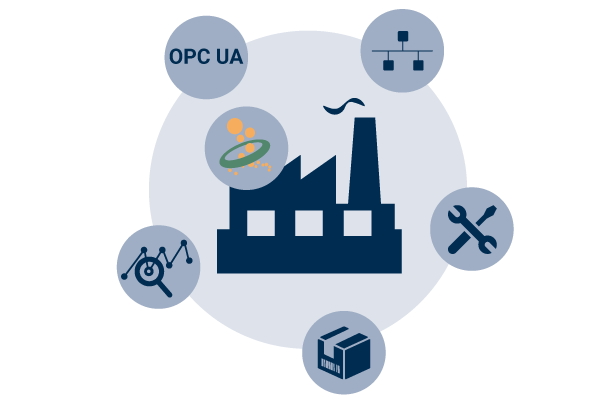
Inhaltsverzeichnis
Inhaltsverzeichnis
1. Cloud
Maschinendatenerfassung gibt es schon deutlich länger als die Cloud-Technologie. Aber die Cloud ist in jedem Fall einer der interessantesten Ziele für Maschinendaten, da das Cloud-Computing viele neue Möglichkeiten und Ressourcen zur Verfügung stellt.
Die Anwendungen in der Cloud sind vielfältig und werden täglich erweitert. Die Datenspeicherung in der Cloud kann in relationalen Datenbanken, NoSLQ Datenbanken und sogenannten DataLakes erfolgen. Grundlegende Anwendungen zur Nutzung der Daten sind Dashboards und Monitoring, und zwar ortsunabhängig. Ein weiteres Anwendungsfeld ist BigData und Maschine-Learning. Hier werden aus den vielen erfassten Daten mit Algorithmen und selbstlernenden Systemen Erkenntnisse gewonnen, die zur Optimierung von Prozessen und zur Erkennung von aufkommenden Fehlersituationen genutzt werden können (Predictive Maintenance).
Die Datenlieferung in die Cloud muss an die technischen Anforderungen des jeweiligen Cloud-Plattform-Betreibers angepasst werden. Viele Plattformen können per MQTT mit Daten beliefert werden, aber zum Teil können auch OPC UA Server als Datenquellen angebunden werden. Nicht zuletzt können auch die Datenbanken direkt beschrieben werden.
Anbindungen an die großen Plattformen haben wir hier dokumentiert:
2. OPC UA
Durch den Kommunikationsstandard OPC UA werden die Mechanismen für den Datenzugriff definiert (s. Was ist OPC UA?). Jede Maschine, jeder Sensor und jedes andere System, dass OPC UA Daten bereit stellt, ist auf gleiche Weise anzubinden. Durch die in OPC UA definierten Mechanismen zur Beschreibung von Datenstrukturen und Datenpunkten, kann eine Maschinendatenerfassung völlig unabhängig von den dahinterliegende Maschinentypen und proprietären Protokollen aufgebaut werden. OPC UA spezifiziert zudem, wie Datenpunkt-Hierarchien aufgebaut und auch durchsucht werden können. Eine Datenbereitstellung von Daten der Fertigung und Produktion, die grundsätzlich auf OPC UA basiert, ist der Schlüssel für eine gute Maschinendatenerfassungs-Infrastruktur, denn sie ist:
- Jederzeit erweiterbar
- Herstellerunabhängig
- Plattformunabhängig
- Interoperabel
- Branchen-übergreifender Standard
3. MQTT
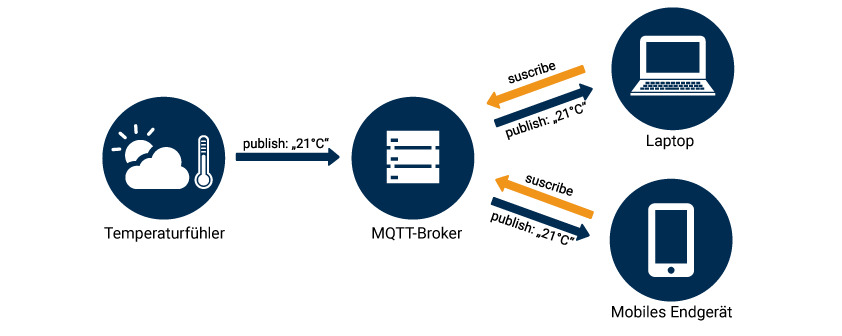
4. Vernetzung
IP-Netze
Um automatisierte Maschinendatenerfassung zu betreiben, ist die Grundvoraussetzung eine durchgängige Vernetzung. In der Industrie hat sich dafür die IP-basierte Vernetzung durchgesetzt. Maschinen und Sensoren müssen also mit Netzwerkkomponenten ausgestattet sein, die den Anschluss an das Netzwerk erlauben. Das Medium, über das die IP Kommunikation läuft, kann durchaus unterschiedlich sein (Ethernet-Kabel, W-LAN, 5G, etc.). Die Fähigkeit von Maschinen zur Netzwerkanbindung ist sehr unterschiedlich. Moderne Maschinen haben Steuerungen, die von Haus aus mit einer Netzwerkanbindung ausgestattet sind. Diese muss dann nur noch aktiviert und konfiguriert werden. Für Neuanschaffungen sollte dies zu einer der Standardanforderungen gehören. Bei älteren Maschinen muss geklärt werden, ob, wie und von wem eine Schnittstelle nachgerüstet werden kann. Für Maschinen, bei denen ein Nachrüsten zu aufwändig oder gar nicht möglich ist, gibt es alternative Lösungen (s. Anbindung von Altsystemen).
Bussysteme
Vernetzungen innerhalb von Maschinen, Anlagen oder Gebäuden, die mit speziellen (nicht IP-basierten) Bussystemen aufgebaut sind, eigenen sich nicht für die Maschinendatenerfassung. Bussysteme wie z.B. Profibus, Profinet, RS458, RS232, KNX, LON, BACNet, MBus, CAN sollten an eine überliegende Steuerung mit Netzwerkanschluss angebunden werden. Alternativ kann eine Hardware-Gateway Lösung eingesetzt werden, welche die Bus-spezifische Physik und Kommunikation auf IP-basierte Kommunikation umsetzt (Zum Beispiel von Wachendorff).
5. Datenspeicherung
Maschinendaten werden im Normalfall gespeichert, um daraus Datenreihen zu generieren, die analysiert werden können. Wo und wie die Daten gespeichert werden, hängt von der Struktur und der Anwendung ab. Werden Daten speziell für ein Zielsystem erfasst, wird das Zielsystem auch die Datenspeicherung selbst übernehmen.
Die sinnvollste Art der Speicherung von Maschinendaten ist die Ablage in einer zentralen Datenbank. Klassische relationale Datenbanken werden hierfür häufig verwendet. In diesen Datenbanken (z.B. Microsoft SQL Server, Oracle, MySQL) werden die Daten in festen Tabellenstrukturen abgelegt und können von dort verschiedenen Zielsysteme bereitgestellt werden.
Neben den relationalen Datenbanken setzen sich auch immer mehr Datenbanken mit neuen Konzepten durch. In den sogenannten NoSQL Datenbanken werden Daten nicht in Tabellen, sondern in losen Strukturen gespeichert, die eine völlig neue Art des Zugriffs, größere Datenmengen und eine hohe Flexibilität in Bezug auf die Struktur der Daten erlauben. Für verschiedene Arten von Daten sind spezielle Datenbanktypen verfügbar (Dokumentenorientert, Graphendatenbanken, Zeitreihen, Key-Value, Multi-Value).
Welche Datenbank konkret verwendet werden sollte, muss mit den Zielsystemen, der Art der Daten und den Verwendungsarten abgeglichen werden.
6. Arten von Maschinendaten
Der Begriff „Maschinendaten“ fasst alle Daten zusammen, die von einer Maschine, typischerweise zur Laufzeit, abgerufen werden können. Was der Inhalt der Daten ist und wie er zu interpretieren ist, kann aber sehr unterschiedlich sein. Grundsätzlich kann die Unterscheidung in einfache Datenpunkte und komplexe Datensätze getroffen werden.
Einfache Datenpunkte, die kontinuierlich oder bei Änderung aufgezeichnet werden, sind Prozessdaten. Diese Daten werden mit dem aktuellen Wert und einem Zeitstempel als Bezug aufgezeichnet und gespeichert. Damit kann der Zustand der Maschinen über die historischen Datenreihen analysiert werden.
Komplexere Daten aus der Maschine werden als zusammenhängende Datensätze aufgezeichnet. Diese Daten enthalten neben dem optionalen Zeitstempel vor allem eindeutige Referenzen auf Datenobjekte, zu denen sie zugehörige Daten liefern. Dies können Produktions- oder Fertigungsaufträge sein oder auch Materialnummern, Maschinennummern, Rezepturnummern, Chargennummern, etc.. Die im Datensatz dazu gelieferten Daten sind dann abhängig von Anwendungsfall. Es können zum Beispiel Prüfergebnisse, Verbrauchsdaten, Fertigwaren-Informationen, Rückverfolgungsdaten und ähnliches sein. Die branchenspezifischen Kommunikationsstandards haben zum Ziel, viele dieser Anwendungsfälle generalisiert zu beschreiben und damit möglichst gleichartige Datensätze Maschinenhersteller-unabhängig zu definieren.
7. Industrie 4.0, IoT und IIoT
Für die Themen Industrie 4.0 und IoT (Internet of Things) bzw. IIoT (Industrial Internet of Things) bildet die Maschinendatenerfassung ein wichtiges Fundament.
Industrie 4.0
Industrie 4.0 beschreibt die vollständige Vernetzung und Kommunikation der Systeme in der Produktion untereinander. Durch die Industrie 4.0-Vernetzung wird es möglich, die Produktion hin zu Selbstoptimierung und Selbststeuerung zu entwickeln. Viele der Daten, die zwischen den Systeme ausgetauscht werden sind Maschinendaten. Eine gut ausgebaute Datenerfassung ist damit eine ideale Ausgangsbasis für Industrie 4.0.
IoT / IIoT
Beim (Industrial) Internet of Things (IoT/IIoT) ist eine wichtiger Anwendungsfall die Übertragung der Zustandsinformationen in die Cloud. Dort wird typischerweise ein digitaler Zwilling abgebildet, der virtuell den gleichen Zustand hat, wie das reale Objekt. Durch eine vorhandene Maschinendatenerfassung kann die Maschine schnell in eine Internet-Plattform integriert werden und das Konzept des digitalen Zwillings für die Maschine realisiert werden.
8. Edge-Computing / Fog-Computing
Durch das Cloud-Computing werden Anwendungen in die in die Cloud verlagert und sind damit nicht mehr direkt im Produktionsnetzwerk verfügbar. Es bleiben aber Aufgaben, die nah an der Produktion, also an der „Edge“, betrieben werden müssen. Daten müssen vorverarbeitet werden, Algorithmen müssen ohne Latenz durch Datenübertragungen der Produktion zur Verfügung stehen und für den Transfer in die Cloud müssen Daten verdichtet werden. Genau dies ist der Bereich des Edge-Computings. Gerade für die Maschinendatenerfassung ist das ein wichtiges Konzept, wenn die Datenerfassung für die Cloud erfolgen soll. Als Plattform für das Edge-Computing gelten kleine integrierte Geräte mit entsprechender darauf laufender Software.
Das Fog-Computing ist im Gegensatz dazu etwas weiter gefasst und beschreibt auch lokal arbeitende Server-Systeme, die sensible Daten verwalten oder Anwendung mit dem Anspruch auf Hochverfügbarkeit betreiben. Das Fog-Computing verbindet aber ebenso den Edge-Bereich und die Cloud.
9. Kosten und Nutzen
Natürlich entstehen für den Aufbau von Maschinendatenerfassung auch Kosten. Diese müssen für die physikalische Vernetzung, die Erweiterung von Steuerungen, Software für die Erfassung und Speicherung und nicht zuletzt für den Arbeitsaufwand für Planung und Umsetzung investiert werden. Aber lohnt der Aufwand?
Der Nutzen der erfassten Maschinendaten ist vielfältig und die Investition lohnt nahezu immer. Gerade die Nutzung der Daten in verschiedenen Systemen für immer neue Anwendungen lässt der Wert der Maschinendatenerfassung ständig steigen. Einige der vielen rentablen Anwendungen sind:
- Automatisierung von manuellen Erfassung
- Optimierungen der Produktionsprozesse anhand der Erkenntnisse aus den Maschinendaten
- Verbesserung von Reaktionszeiten innerhalb der Produktion durch schnelle Information
- Genauere Planungsmöglichkeiten für Personal und Rohstoffe durch genauere Zeiterfassung und Materialverbauchsmeldungen.
- Vermeidung / Verkürzung von Maschinenausfällen durch sofortige Störmelde-Verteilung
- Besserer Kundenservice durch genauere Informationen über Lieferzeiten
- Optimierung der Maschineninstandhaltung durch genauere Wartungszyklen-Einhaltung und Predictive Maintenance
- u.v.a.m.
10. Sicherheit
Wird eine Maschine für die Maschinendatenerfassung vernetzt, muss von Anfang an auch die IT Sicherheit bedacht werden. Denn mit der Vernetzung ist eine Maschine in jedem Fall angreifbarer, als ohne Vernetzung. Das ist ein Fakt. Aber es gibt sehr viele Möglichkeiten, die entstehenden Risiken auf ein Minimalmaß zu reduzieren, indem allgemein gängige Sicherheitsmechanismen genutzt werden.
Netzwerktrennung
Die grundlegendste Absicherung von unauthorisierten Zugriffen ist eine strikte Netzwerktrennung. Es muss klar unterschieden werden, welche Netzwerkbereiche es gibt, wie sie verbunden werden und welche Kommunikation zwischen den Netzen erlaub wird. Die Umsetzung erfolgt mit einer Firewall. Für Produktionsnetze sind auch Lösungen verfügbar die das Produktionsnetz als solches nochmals segmentieren und einzelne Produktionsinseln gesondert abschotten. Nur die für die Maschinendatenerfassung benötigten Pfade werden für definierte Clients geöffnet.
Zertifikate
In den standardisierten Kommunikationsprotokollen gibt es zudem integrierte Mechanismen, um die Sicherheit der Datenerfassung zu garantieren. So ist im Konzept von OPC UA Sicherheit als Standard-Anforderung umgesetzt worden. Neben der verschlüsselten Übertragung ist bei OPC UA auch ein Zertifikatsaustausch zwischen Client und Server vorgesehen. Viele andere Protokolle stammen leider aus einer Zeit, in welcher der Fokus noch nicht auf Sicherheit lag, so dass hier integrierte Mechanismen fehlen und immer zusätzlich konfiguriert werden müssen. OPC UA ist daher auch aus der Perspektive „Sicherheit“ eine gute Wahl.
Zugriffssteuerung
Nicht zuletzt ist auch bei der Maschinendatenerfassung eine Benutzerauthentifizierung notwendig, um den Zugriff auf die Daten nach Rollen zu beschränken. Für die modernen Systeme zur Speicherung der Daten (Datenbanken / Cloud) sind diese Funktionalitäten Standard und müssen nur aktiv genutzt werden.
11. Kommunikationsprotokolle
Proprietär
In der Fertigung und Produktion findet sich meist ein heterogener Maschinenpark und zusätzlich eine Vielzahl intelligenter Sensoren und Geräte. Die Kommunikationsprotokolle, die zur Datenabfrage über die IP-basierte Kommunikation gesprochen werden, können proprietäre oder standardisierte sein.
Bei einem proprietären Protokoll hat der Hersteller ein eigenes Protokoll definiert. Dadurch werden alle speziellen Möglichkeiten der Datenquelle zugänglich gemacht und die Kommunikationsgeschwindigkeit ist im Optimalfall hoch optimiert. Das spezielle Protokoll muss allerdings auch für die Maschinendatenerfassung vom Client implementiert werden, um die Daten anzubinden. Um auf solche Steuerungen und Geräte zuzugreifen eigenen sich besonders Software-Komponenten, welche die proprietären Protokolle schon fertig implementieren und in ein standardisiertes Protokoll übersetzen. Ein gutes Beispiel dafür ist der Kepware OPC Server, der mit über 160 Treibern viele dieser Protokolle spricht und dann unter anderen in OPC UA wandelt.
Standardisiert
Die standardisierten Protokolle sind von Verbänden und Konsortien definiert worden, um die Nachteile der proprietären Protokolle zu vermeiden und ein einfaches Verbinden von Datenquellen und Datensenken zu ermöglichen. Neben recht Hardware-nahen Standards wie ModbusOnTCP oder BACNet/IP haben sich große und verbreitete Standards etabliert wie MQTT, MTConnect und OPC UA. MQTT ist dabei primär im IoT Umfeld zu finden. MTConnect ist speziell für Werkzeugmaschinen entwickelt und vor allem in Nordamerika verbreitet. Für die Maschinendatenerfassung hat sich für die Industrie in den letzten 20 Jahren der OPC Standard durchgesetzt. Immer mehr Steuerungen und Geräte stellen OPC UA als Kommunikationsprotokoll direkt bereit. Für andere gibt es die Umsetzung von proprietären Protokollen auf OPC UA mit entsprechenden OPC Servern. Wird OPC UA als kleinster gemeinsamer Nenner für die Datenerfassung definiert, können alle Datenquellen und Clients darauf ausgerichtet werden und dadurch eine erweiterbare und standardisierte Maschinendatenerfassung aufgebaut werden.
12. Kommunikationsstandards
Neben der reinen Standardisierung der Kommunikationsprotokolle, gibt es in vielen Industrien auch Bestrebungen, die Datenstrukturen zur Maschinendatenerfassung zu standardisieren. Verschiedene Arbeitsgruppen haben gemeinsam festgelegt, welche Daten in welcher Form mit Maschinen ausgetauscht werden. Beispiele hierfür unter vielen anderen sind EUROMAP 63 (Spritzguss), Weihenstephaner Standard (Getränke), PackML (Verpackung), IEC 61850 (elektr. Schaltanlagen). Implementiert eine Maschine den entsprechenden Industrie-Standard, ist sichergestellt, dass bestimmte Daten von der Maschine bereitgestellt werden. Die Detailabstimmung und Festlegung von Schnittstellen auf Datenpunkt-Ebene entfällt und der Aufbau der Datenerfassung wird stark beschleunigt.
Eine Kombination aus Industrie-spezifischen Standards und dem standardisierten Kommunikationsprotokoll OPC UA bilden die seit kurzen vorangetriebenen Companion Specifications der OPC Foundation. Die Vorteile werden in den Specifications vereint, so dass von einer Maschine vordefinierte OPC UA Datenpunkt-Strukturen erwartet werden können, wenn sie eine Companion Specification implementiert. Beispiele hierfür sind EUROMAP 77 (Spritzguss), OPC UA PackML (Verpackung), AutoID (Ident), Umati (CNC), IEC 61850 (elektr. Schaltanlagen ). An vielen weiteren wird derzeit gearbeitet.
13. Anbindung von Altsystemen
Nicht alle Maschinen lassen sich einfach in eine moderne Vernetzung aufnehmen. Vor allem ältere Maschinen sind schwierig einzubinden. Die Gründe sind häufig:
- keine Steuerung vorhanden, rein mechanische Maschine bzw. nur einfache Elektronik
- Steuerung kann nicht um eine Netzwerkanbindung erweitert werden
- Kosten, Aufwand und Risiko zu hoch für Netzwerknachrüstung
- Fehlendes Know-How für Nachrüstung
Sind die Maschinendaten einer solchen Anlage aber trotzdem wichtige Informationen, können viele Daten durch Kleinsteuerungen erfasst werden. Diese werden an oder in die Maschinen verbaut. Kleinsteuerungen, wie zum Beispiel von WAGO (PFC200), Beckhoff (Embedded PC) oder Siemens (S7-1200), können mechanische Zustände und Vorgänge über Sensoren erfassen und zählen, es können aber auch elektrische Signale über Verkabelungen an das Altsystem abgegriffen werden. Als Schnittstelle für die Maschinendatenerfassung verfügen die Kleinsteuerungen alle über OPC UA und integrieren sich damit perfekt in die standardisierte Infrastruktur.
14. Zielsysteme
Maschinendatenerfassung dient der Transparenz des Produktionsprozesses. Die Datenerfassung als solche kann immer unabhängig betrachtet und aufgebaut werden. Durch die Weitergabe der Daten an Zielsysteme ergeben sich dann aber erst höhenwertige Erkenntnisse und Anwendungsmöglichkeiten. In der Produktion und Fertigung gibt es verschiedene Systeme, die dafür verwendet werden, die Produktion zu steuern, zu beobachten und zu planen. Welche Systeme zum Einsatz kommen, ist abhängig von Branche und Größe der Produktion. Oft sind diese Systeme zu finden:
- ERP (Enterprise Ressource Planning)
- MES (Manufacturing Execution System)
- Qualitätssicherung
- EnMS (Energiedaten)
- Instandhaltung / Wartung
- Reporting
Jedes dieser Systeme ist abhängig von Informationen aus der Produktion und kann effizienter Arbeiten, wenn Daten aus der Maschinendatenerfassung automatisch in das System einfließen, anstatt durch manuelle Vorgänge eingepflegt zu werden.
15. OEE – Overall Equipment Efficency
Die OEE Kennziffer ist ein spezieller Anwendungsfall der Maschinendatenerfassung. Für den OEE sind feste Formel und Datenpunkte vorgegeben, die zur Berechnung herangezogen werden. Der OEE ist das Produkt aus drei Einzelfaktoren:
OEE = Nutzungsgrad (NG) x Leistungsgrad (LG) x Qualitätsrate (QR)
Nutzungsgrad = Real verfügbare Zeit / Planbelegungszeit
Der Nutzungsgrad beschreibt dabei das Verhältnis zwischen geplanter Betriebszeit der Maschine zur tatsächlichen Betriebszeit, ohne die Zeiten in der die Maschinen wegen Störungen und ähnlichem ausgefallen war. Für die Maschinendatenerfassung stellt die Maschine im besten Fall ein Signal bereit, das die Betriebsbereitschaft signalisiert und welches dann aufgezeichnet werden kann, oder es werden Störungen aufgezeichnet, deren zeitliche Dauer dann als Ausfallzeit abgerechnet wird.
Leistungsgrad = Ist-Produktionsmenge / Sollproduktionsmenge (Taktrate x Maschinenlaufzeit)
Um den Leistungsgrad zu ermitteln, wir die tatsächliche Leistung der Maschinen anhand der Ausbringungsmenge durch die Soll-Menge geteilt. So ergibt sich, wieviel von der erwarteten Produktionsleistung prozentual erbracht wurde.
Qualitätsrate = Gutmenge / Gesamtmenge
Die Qualitätsrate setze die Anzahl qualitativ guter Produkte mit der Gesamtproduktionsmenge inklusive Ausschuss ins Verhältnis.
16. Praxisbeispiele
Beispiele aus der Praxis zeigen am besten die Motivation und den Nutzen für realisierteMaschinendatenerfassungen. Lesen Sie hier Berichte von unseren Kunden:
- Automobilzulieferer Auria Solutions
- Kettensägenhersteller Stihl
- Farbmess- und Regelsysteme XRrite
- Milchwerk DMK Altentreptow
- Etikettenhersteller HERMA
Einfache Maschinendatenerfassung in der Praxis
In der Praxis kann Maschinendatenerfassung die Produktion eines Unternehmens optimieren. Mit der erlangten Transparenz werden Daten erfasst, gespeichert und ausgewertet sowie eine bessere Produktionssteuerung erreicht.
Die erfassten und gespeicherten Daten können von verschiedenen Abteilungen genutzt werden. Die Produktionsabteilung überwacht in Echtzeit die aktuelle Produktionsgeschwindigkeit und greift gegebenenfalls frühzeitig in die Produktion ein. Somit kann die Produktionsauslastung verbessert oder auch Produktionsstopps verhindert werden. ERP Systeme wie SAP oder Web Services können zusätzlich die Maschinendaten erfassen und auswerten. Somit profitieren davon andere interne Abteilungen wie beispielsweise das Controlling oder die Logistik und werden automatisch über abgeschlossene Aufträge informiert oder mit aktuellen Daten versorgt. Eine Maschinendatenerfassung in Echtzeit, realisierbar mit Software wie dem OPC Router, bietet eine unternehmensweite Transparenz, ermöglicht eine Produktionssteuerung in Echtzeit und optimiert jede Produktion.
Weitere Informationen
Erfahren Sie mehr über Industrie 4.0! Die vierte industrielle Revolution durch Digitalisierung: Menschen, Maschinen und Produkte sind direkt miteinander vernetzt. In unserem Beitrag lesen Sie mehr!
Mit OPC UA wird ein standardisierter Zugriff auf Maschinen, Geräte und andere Systeme in der Industrie 4.0 ermöglicht und so ein herstellerunabhängiger Datenaustausch gewährleistet. In unserer Knowledge Base finden Sie einen Überblick über Funktionalität und Begriffe des wichtigsten Kommunikationsprotokolls für die Industrie 4.0 und das Industrial Internet of Things (IIoT).
Der OEE (Overall Equipment Effectiveness) misst die Effektivität in den Bereichen Verfügbarkeit, Leistung und Qualität. Die OEE-Kennzahl ermöglicht einen Überblick über die Gesamtanlageneffektivität und zeigt Optimierungsmöglichkeiten auf. Erfahren Sie in unserem OEE-Beitrag alle wichtigen Grundlagen und wie sie den OEE berechnen, um Ihre Produktion zu verbessern.
Weitere interessante Artikel zu den Themen Industrie 4.0, Cloud, Technik, Alarmierung und praktische Anwendungsbeispiele sowie Case Studies finden Sie in unserer Knowledge Base.